The Project
A customer in the quarrying and Asphalt sector was experiencing high rates of abrasion in aggregate dryer drums. This was leading to increased downtime for refitting and lost production, and of course the higher the demand for their product the higher the incidence and effect of disruption to this ideally 24/7 process.
Need/Requirement
A better material grade was required to be identified to form the lifters in the aggregate drying drums. The aggregate material within the drums heats up not only to dry the aggregate but so bitumen can bond to the aggregate producing asphalt. A level of corrosion resistance would be required in addition to wear properties. The original allegedly ‘high wear resistant’ components were a specialist supply to the customer from the plant manufacturer so Brown McFarlane would need to reverse engineer the components to produce a technical drawing for customer approval and profile production. Bending and end cap welding would also be required to be performed.
Specialist Skills
Sourcing the correct grade of material for wear and corrosion resistance was critical Accurate CAD, profiling and forming capability was an important consideration to ensure the new lifter components fitted perfectly for ease of assembly, perfect plant operation and minimal downtime.
Capability
Brown McFarlane’s access to material and skills required to perfectly execute this project are known around the world. Our latest technology includes the Infinity Skew Head Plasma Bevel Cutter, Bystronic Water Jet profiling, Laser Cutting and demonstrates Brown McFarlane’s long held strategy of being the industry leader in technology and innovation.
Brown McFarlane’s 100000sqft facility is capable of storing , handling and processing massive tonnages of steel plate. A mixture of more traditional and state of the art Oxy and Plasma equipment means we have the capacity as well as the skills, experience and quality standards to meet the customers requirement.
The Agreed Solution Scope
Brown McFarlane would use its extensive experience of high wear application material to source and supply the right material. In this case Quard 400HB was selected as steel plate with the optimal characteristics in the correct sizes for processing with minimal scrap.
Two lifter components 16 of each would be prepared, both required bending and one type would require end caps. A 50% reduction in component wear was expected.
The material would be profiled to exact size at Brown McFarlane’s first class profiling facility in Stoke on Trent UK. Delivery would be to the customer’s site to fit in with the scheduled maintenance routine.
We quickly established a gas profiling solution that would give the appropriate tolerances and the appropriate Quality Control processes required at all process stages.
Additional Customer Requirements
Special attention was also paid to providing a value for money solution for the customer. Not only in reducing down time but ease of ‘weld in’ of the selected product as they intended to perform the installation themselves.
The Steel Solution
The material was supplied quickly from our extensive range of wear material stocks. Worn items to be replaced were supplied to us for examination and accurate CAD drawings prepared for customer sign off. Steel was profiled and processed into the finished lifter components to schedule and supplied to fit the maintenance schedule.
The Delivery
Due to Brown McFarlane’s own, extensive know how, coupled with our extensive Western European sourced steel stocks; we were able to provide a materials solution to the customer that completely met with the required specification. On top of this, we were able to provide accurate, cut to size parts, which were delivered to the customers exacting requirement saving the customer time, space and money.
The Conclusion
Another satisfied customer! By our ability to react instantly and our unique range of high specification steels meant a major pipeline closure at a critical time of the year was averted.
Regrettably many replacement wear parts are provided with less than optimal corrosion and wear resistant properties. While many manufacturer supplied wear items that are cheap to source and manufacture, often end users see no cost benefit as prices are similar to fabrication of technically better and longer lasting components. The plant manufacturer providing the part sees the benefit in higher wear part margins and increased sales volumes. The end user experiencing higher bills and more frequent downtime of revenue generating plant.
With increasing skills shortages and leaner workforces the ability to instantly bring traditional or sophisticated processing to the highest quality standard on demand is something our customer understands and recognises as a vital part of solution provision and maintenance planning.
All this is another example of our commitment to our customers and demonstrable proof of our ability to assist in the delivery of innovative solutions in full and on time. Other applications that would be useful in sand and aggregate production include liners, feeders, screens, hoppers and chutes. This can be used for wear strips and bucket edges.
Related News
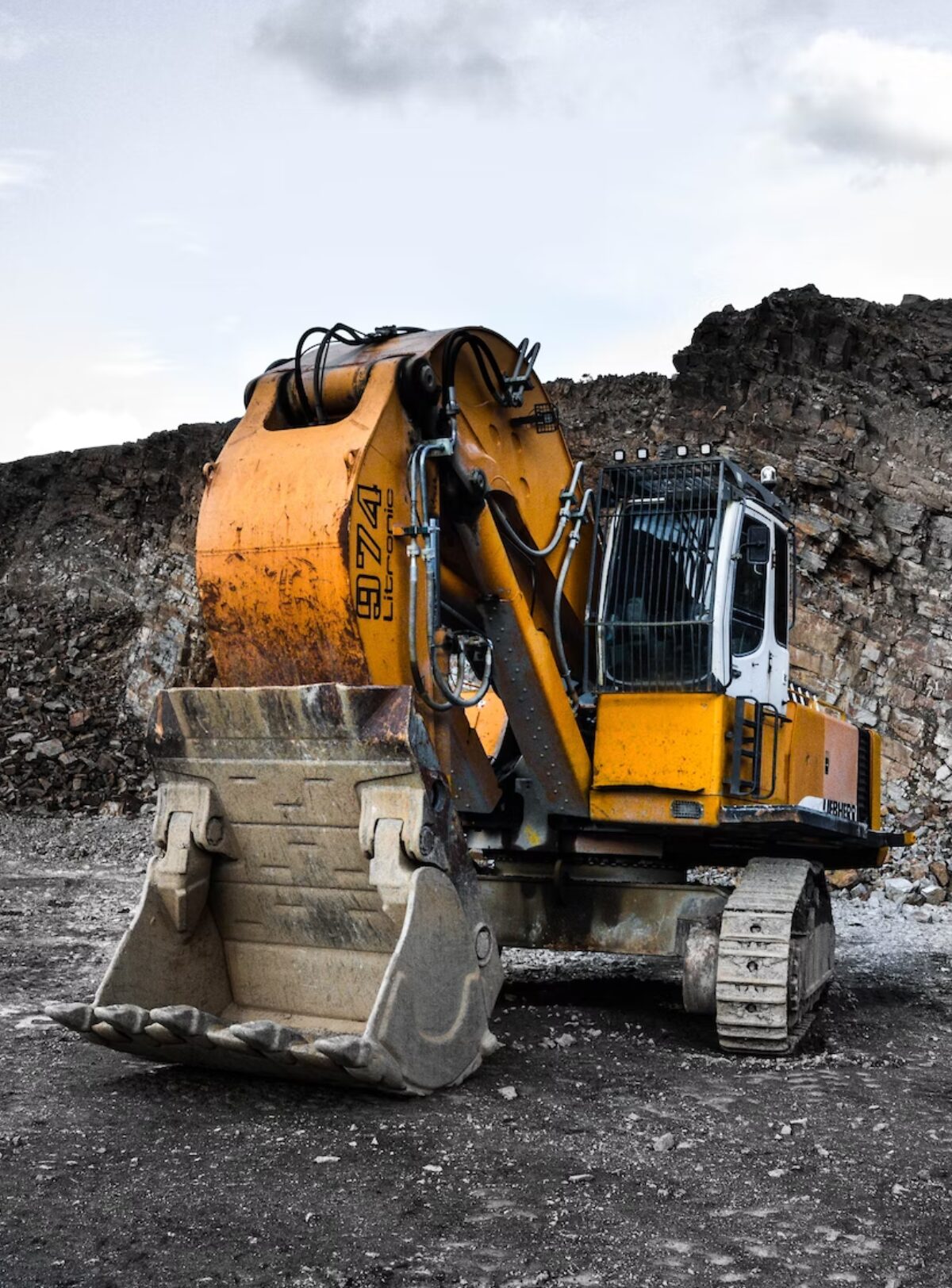
Which Industries Use Creusabro Abrasion Resistant Plates?
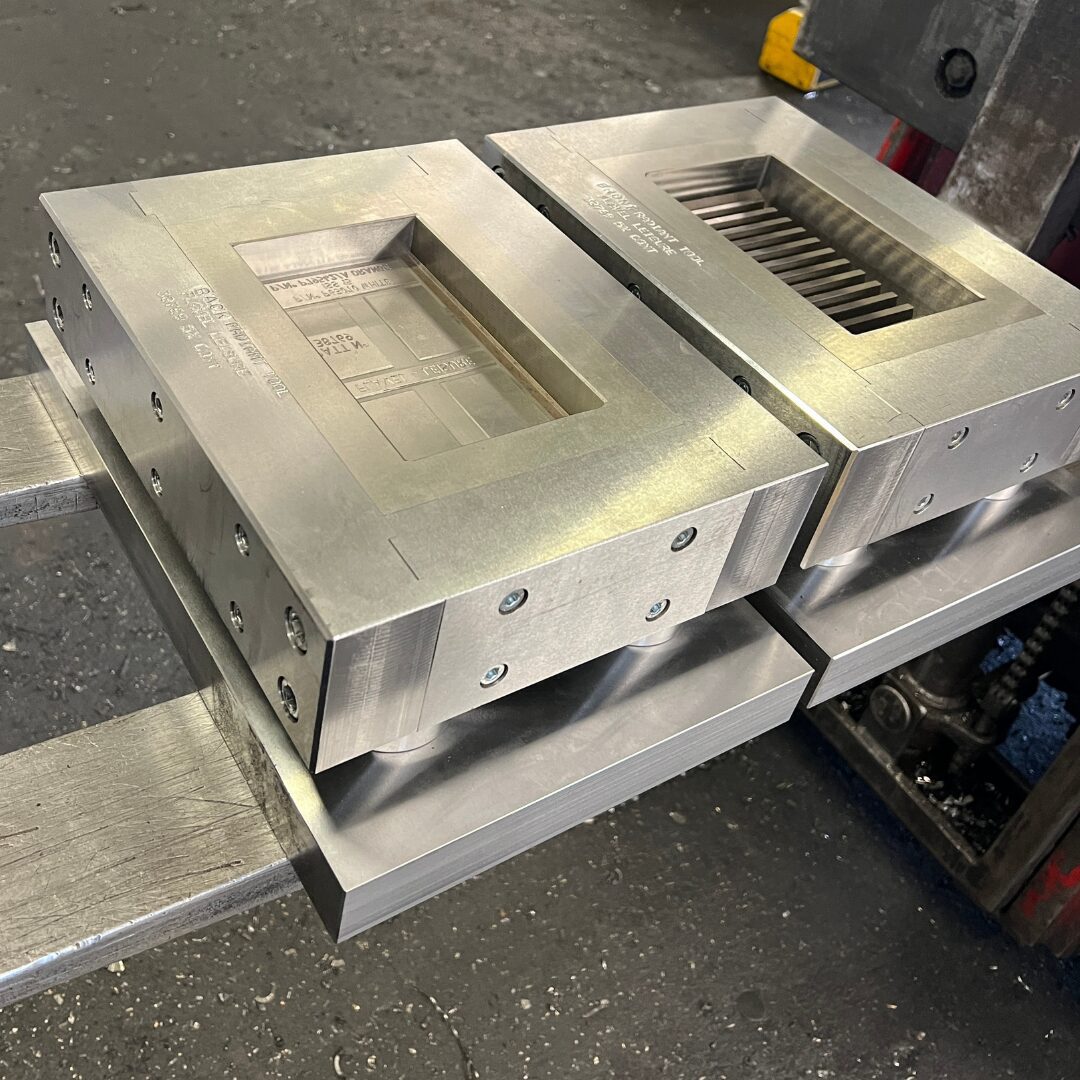
Steel Plate Processing for Custom Industrial Components
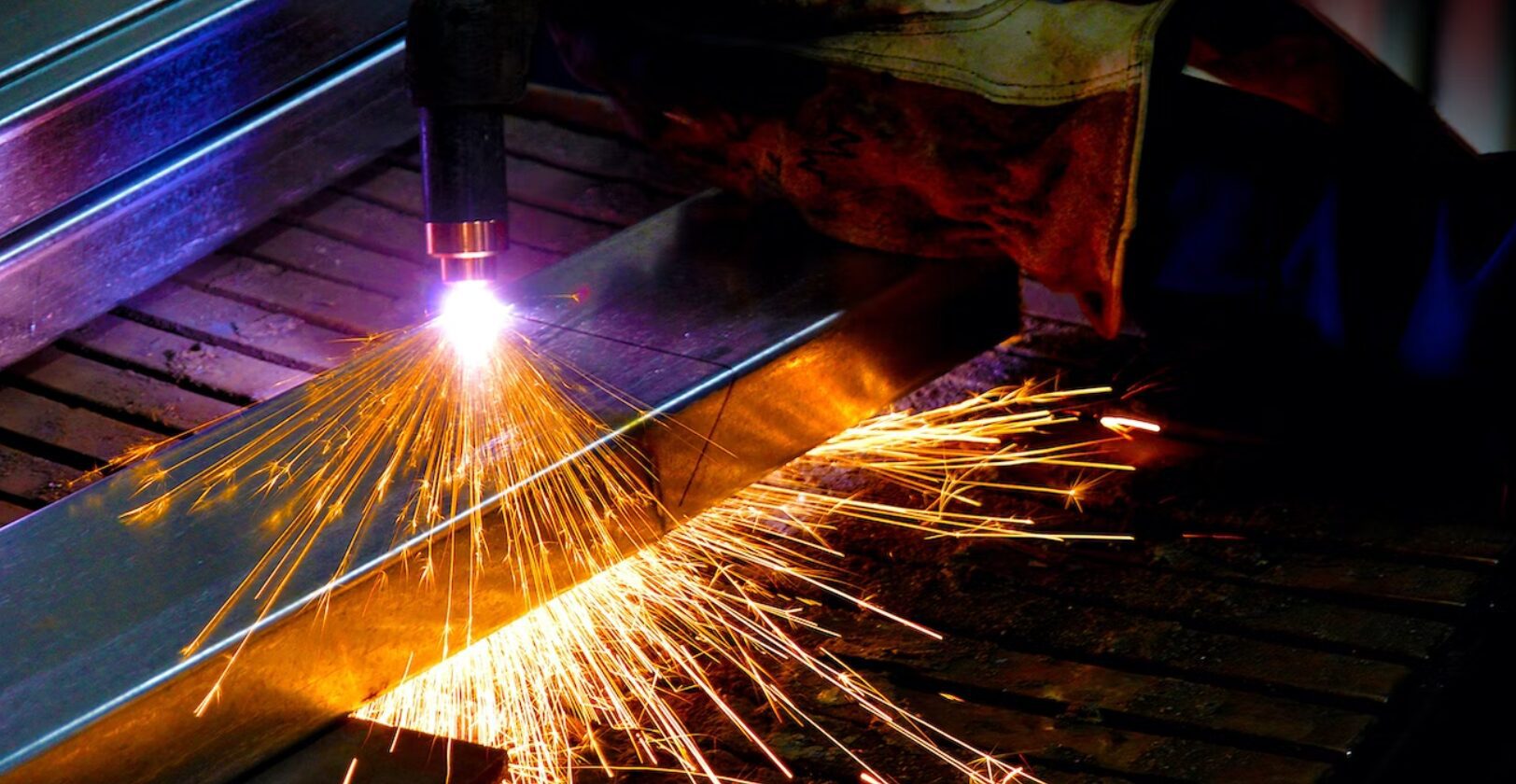