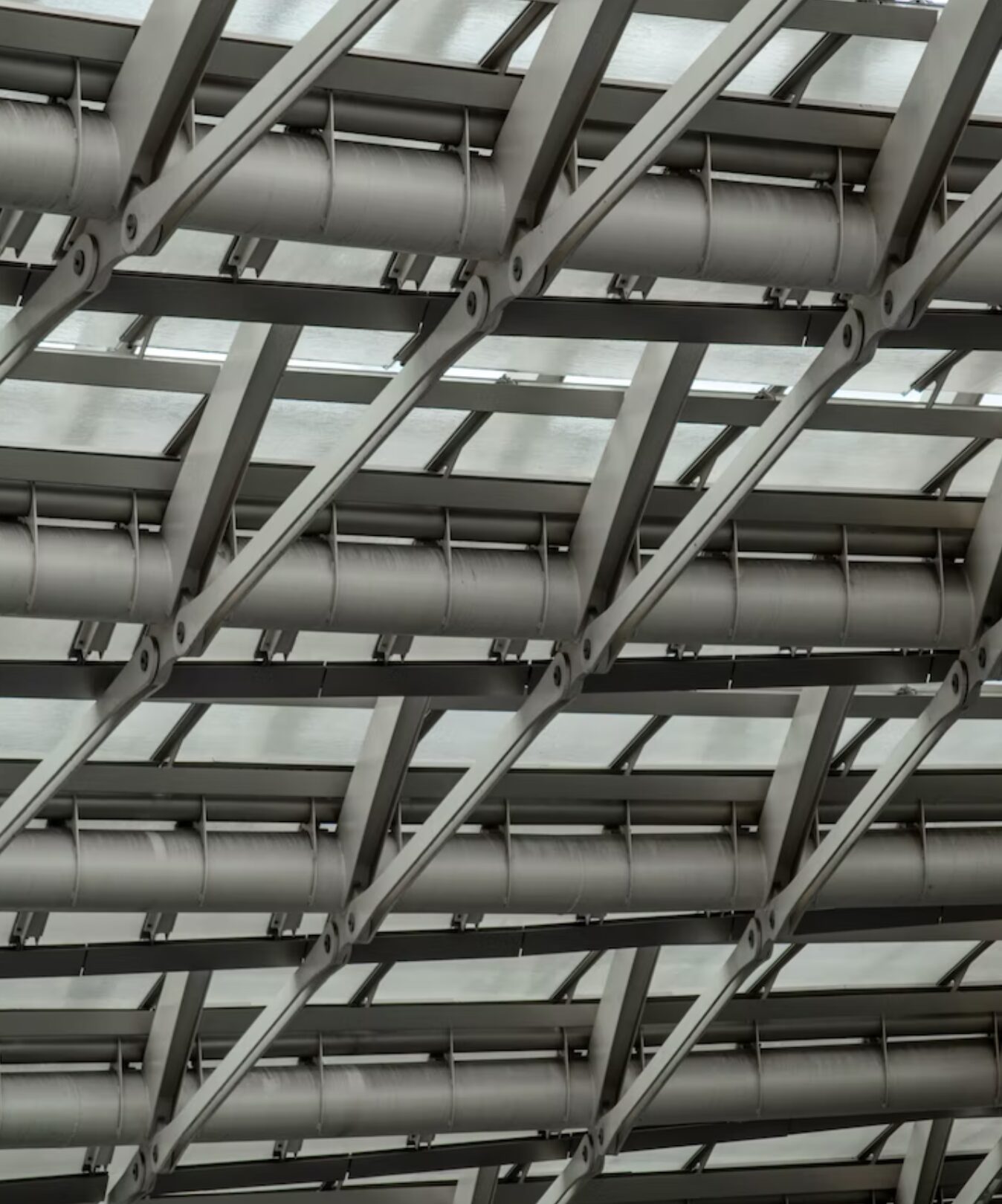
Steel plate rolling involves passing a piece of steel plate through one or more pairs of rollers in order to reduce the overall thickness of the material. This process also ensures that the workpiece thickness is unchanging throughout. This procedure is categorised according to the temperature of the steel plate being rolled. If the temperature is above recrystallization point the process is called hot rolling and if below it is called cold rolling.
More information
-
Hot Rolling
Hot rolling processes more weight than any other manufacturing process available. Finished products are usually of a very high quality but can be left covered in mill scale due to the high-temperatures during processing. This oxide is removed via pickling to leave behind a smooth surface. This method is usually employed to produce sheet metal or other materials, including:
• Automotive parts (frames, wheels, water heaters etc.)
• Agricultural equipment
• Compressor shells
• Metal buildings
• Guard rails -
Cold Rolling
Cold rolling increases a material’s strength, improves the surface finish and maintains tighter tolerances. However, cold rolling cannot reduce the thickness of a material as well as hot rolling can, especially in a single pass. Cold rolled sheets and strips come in various conditions:
• Full-hard
• Half-hard
• Quarter-hard
• Skin-rolled -
Full-hard cold rolling
Full-hard cold rolling reduces a material’s thickness by up to 50%. Each respective condition then reduces less thickness as we go down the list, finishing with skin-rolling that reduces thickness by no more than 1%. This last condition is used more commonly to provide a uniform finish. Common applications of cold rolling include smaller parts such as:
• Metal furniture
• Motorcycle parts
• Lighting fixtures
• Hinges